1、修炉材料的选用标准
a.修炉用硅砂的化学成分要求,见表1。
表1 修炉用硅砂化学成分 |
成分 | SiO2(%) | Fe2O3 (%) | 附着水分(%) |
含量 | ≥99 | ≤0.05 | ≤0.5 |
b.修炉用硼酸的化学成分要求,见表2。
表2 修炉用硼酸的化学成分 |
成分 | P2O2(%) | 结晶粒度(毫米) | 附着水分(%) |
含量 | ≥98 | ≤0.5 | ≤0.5 |
c. 修炉用镁砂的化学成分要求,YB415-63 类-等,见表3。
表3:修炉用电熔镁砂的化学成分 |
成分 | MgO | 杂 质 | 灼烧减量 |
SiO2 | Fe2O3 | CaO |
含量(%) | ≥90 | ≤4 | ≤1 | ≤2.5 | ≤1.0 |
2、坩埚模
坩埚模用3mm 钢板制作,见图1。
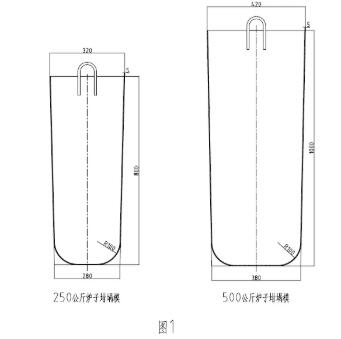
3、修炉材料配比
(1)酸性炉衬材料配比,见表4。
表4:酸性炉衬材料配比 |
编号 | 硅砂(粉)分组代号(目)(%) | 硼酸 (外加%) | 水 (外加) |
(4/5) | (6/10) | 60(20/40) | 21(50/100) | 05(200/270) |
1 |
| 30 | 50 | 10 | 10 | 2 | 适量 |
2 | 25 | 20 | 30 |
| 25 | 1.5~2.0 | 适量 |
|
|
|
|
|
|
|
|
(2)酸性炉领材料配比,见表5。
表5:酸性炉领材料配比 |
编号 | 硅砂(粉)(mm) | 水玻璃 (外加) | 水 (外加) |
1~2 | 0.2~0.5 | <0.1 | <200(目) |
1 | 30 | 50 |
| 20 | 10 | 适量 |
2 | 30 | 40 | 20 | 10 | 10 | 适量 |
|
|
|
|
|
|
|
(3)碱性炉衬材料配比,见表6。
表6:碱性炉衬材料配比(%) |
编号 | 电熔镁砂(mm) | 耐火粘土 | 硼酸 (外加) | 水 |
4~2 | 2~1 | <1.0 |
2 | 20 | 50 | 30 | 2-2.5 | 1.5~2.0 | 适量 |
|
|
|
|
|
|
|
(4)碱性炉领材料配比,见表7。
表7:碱性炉领材料配比 |
电熔镁砂(旧炉壁回收砂) | 白坭 | 水 |
65% | 35% | 适量 |
(5)感应器保护材料配比,见表8。
表8 感应器保护材料配比(%) |
编号 | 硅石粉 11号筛(270目) | 石棉粉 | 耐火粘土 | 矾土水泥(400-500#) | 水 |
1 | 50 | 30 | 20 |
| 适量 |
2 | 80 |
|
| 20 | 适量 |
3 |
|
| 80 | 20 | 适量 |
4、修炉操作要点
|
序号 | 工序名称 | 操作要点 |
1 | 筑炉准备 | 1.用0.2至0.3 MPa的水压检查感应器是否有渗漏现象,感应圈匝之间绝缘是否良好。 2.按要求配制感应器膏状保护料,均匀涂铺于感应器上,自然干燥24小时或烘干。 3.按照要求配制好筑炉材料,并混合均匀。在混合前,应用磁铁检查并除去材料中的铁销;在混合过程中要防止沙土、铁销和其它杂物混入。 |
2 | 筑炉 | 1.筑炉底 a.在炉底石棉板上,每次铺以20到50mm高的炉衬材料,用撞锤捣固紧实,直至平面超出感应圈之最底圈20到30mm b.换以圆形筑炉棒打压,使表面坚固,再用耐火砖抹平,直至要求高度 2.筑炉壁 a.将坩埚模(在外壁包以厚纸板)置于感应圈同心位置,定位后用钢料压紧和固定,然后筑炉。 b.将坩埚底部炉衬材料用叉状棒拨弄粗糙,每次装入20-40mm炉衬材料捣实,直至离炉顶50mm,即感应圈匝上边缘为止。 3.筑炉领 按要求配制炉领材料,打结炉领和出铁槽,并用水玻璃溶液(水+水玻璃=1:1)均匀涂刷于表面 |
3 | 烧结 | 1.打结坩埚自然干燥大于16小时后即可进行烘烤。 2.烧结时,在坩埚内装入金属料,分级缓慢送电加热(30kw,1小时;40kw,2小时;50kw,2小时,60kw)炉内温度约在700-800℃保持8-10小时,然后逐步加大功率,使金属熔化,并在1700℃保持1小时烧结 3.烧结完的坩埚,可以继续熔炼或停炉,以原冷却水的2/3冷却炉衬3-4小时待用。 |
5、浇包包衬搪制
(1)包壳用3mm 钢板制作。
(2)包衬材料配比,见表10,
表10 包衬材料配比 |
石英砂或镁砂(%) | 耐火土(%) | 硼酸(%) | 水(%外加) |
97~96 | 2~2.5 | 1~1.5 | 3~5 |
(3)搪好的浇包,在表面涂水玻璃,自然干燥4小时以上,使用前再在900±50℃烘烤3小时以上。
文章转自热加工论坛
上一篇:提高电炉熔炼铸铁的一些注意事项
下一篇:铁型覆砂铸造工艺防止铸件缩孔缩松的各种方法及其成功案例
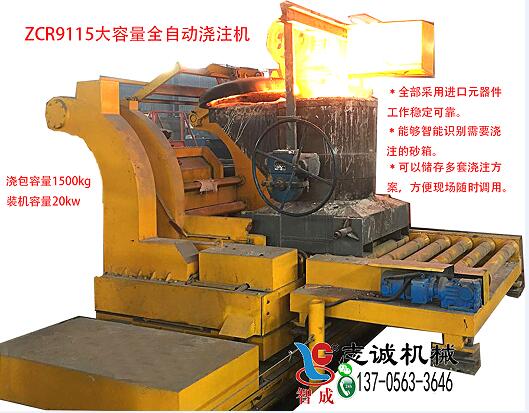
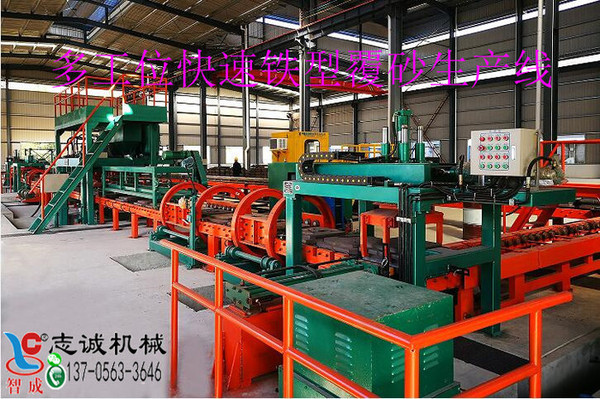